Stamping and bending parts

Automotive E‑Mobility Medical Leisure Industry
STRIP/STAMPING AND BENDING PARTS
One of the most variable products: Stamped and bent parts from strip material
Function:
Application-specific strip/punched bent parts with a wide range of functions
Description:
Stamped and bent parts made from strip material in coils are fed through the die as a “strip”. For example, stamped and bent parts in the wheel brake area.
Advantages
- Many years of know-how in the field of stamping and bending technology. (spring steel, non-ferrous metals, cold-rolled strip)
- Functional integrations implemented many times
- Various joining techniques (material or form-fit: welding or pressure joining)
Innovation
- Economical use of material through efficient punching strip design
- Modular tools
Production
- In-house prototype construction
- In-house process and development
- Extensive laboratory facilities for the development of innovations (incl. failure analysis and fatigue tests)
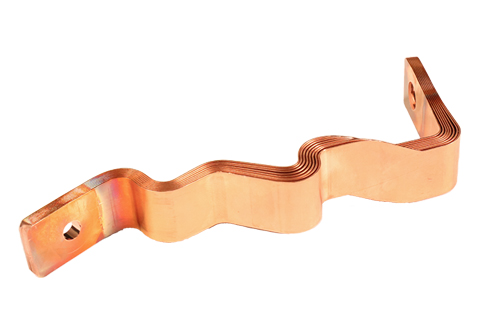
E-mobility
Flexible Busbars
Flexible busbars are the ideal solution for thermally and mechanically stressed system interfaces.
Function:
Unlike rigid busbars, the flexible multilayer busbar help to decouple systems and compensate operational length changes.
Description:
Multilayer copper busbars for battery module connectors, e‑motor interface and other e‑mobility busbar applications.
Advantages
- Compensation of system movements
- Tolerance compensation
- Multi-Position parts
Innovation
- Redesign of rigid busbars into flexible busbars
- Mechanical and electrical tests
- Process for high volume production
Production
- Stamping/bending techniques
- Laser welding
- Resistance welding
- Diffusion welding
- Surface coatings
- Press-fit technology
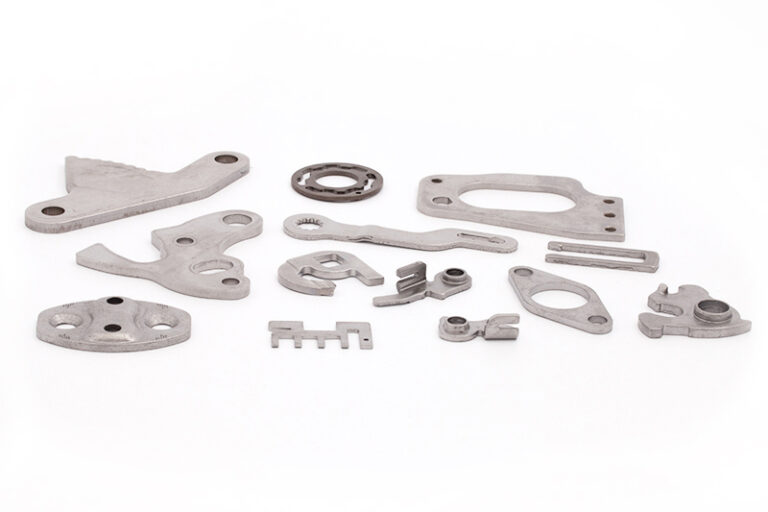
Automotive
FINE-BLANKING PARTS
FINE-BLANKING PARTS ARE CHARACTERISED BY EXTREMELY PRECISE RIGHT-ANGLED AND TEAR-FREE CUTTING SURFACES
Function:
Fine-blanking parts in highest accuracy for different applications.
Description:
The fine-blanking process allows a very smooth cutting quality at the cutting surface. Furthermore, massive forming and bending processes can be integrated into the fine-blanking process. Due to complete or local quenching and tempering processes, wear-reducing or resilient loads can be integrated.
Advantages
- Functional integration
- Highest mechanical load
- Weight reduction
- Use for dynamic load and high temperatures
Innovation
- Local hardening
- Flatness and dimension optimized quenching and tempering
- Use of SOF processes
Production
- Forming simulation
- In-house prototype construction
- Fatigue strength tests
- Relaxation tests
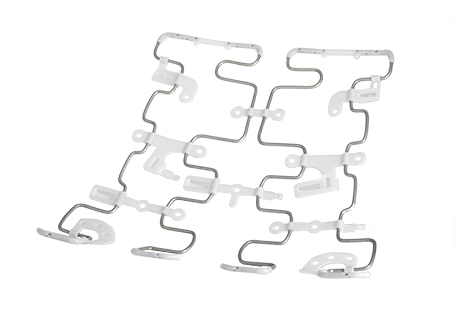
Automotive
PLASTIC METAL COMBINATIONS
THE PRODUCTION OF HYBRID COMPONENTS FROM METAL PLASTIC COMBINATIONS OPENS A WIDE RANGE OF POSSIBILITIES FOR PRODUCT DESIGN
Function:
Direct combination of plastic and metal without additional joining partners.
Description:
Using the outsert technology different products can be produced as hybrid plastic-metal combinations. The advantages of both material classes complement each other in an optimal way.
Advantages
- Complex assembly components can be represented as parts that fall off the mold
- Functional integration
- Weight saving
- High automation possible
Innovation
- Mold Flow Analysis
- FEM-aided design
Production
- Plastic injection molding
- Surface coating
- Assembly operations (automated)